Health and Safety
At NIKE, we believe having a safe and healthy work environment is a fundamental human right.
In line with the ILO’s Declaration on Fundamental Principles and Rights at Work, we strive to provide workplaces that uphold that right throughout our operations. As part of a responsible supply chain, we expect suppliers to advance similar workplace standards for those who make our products.
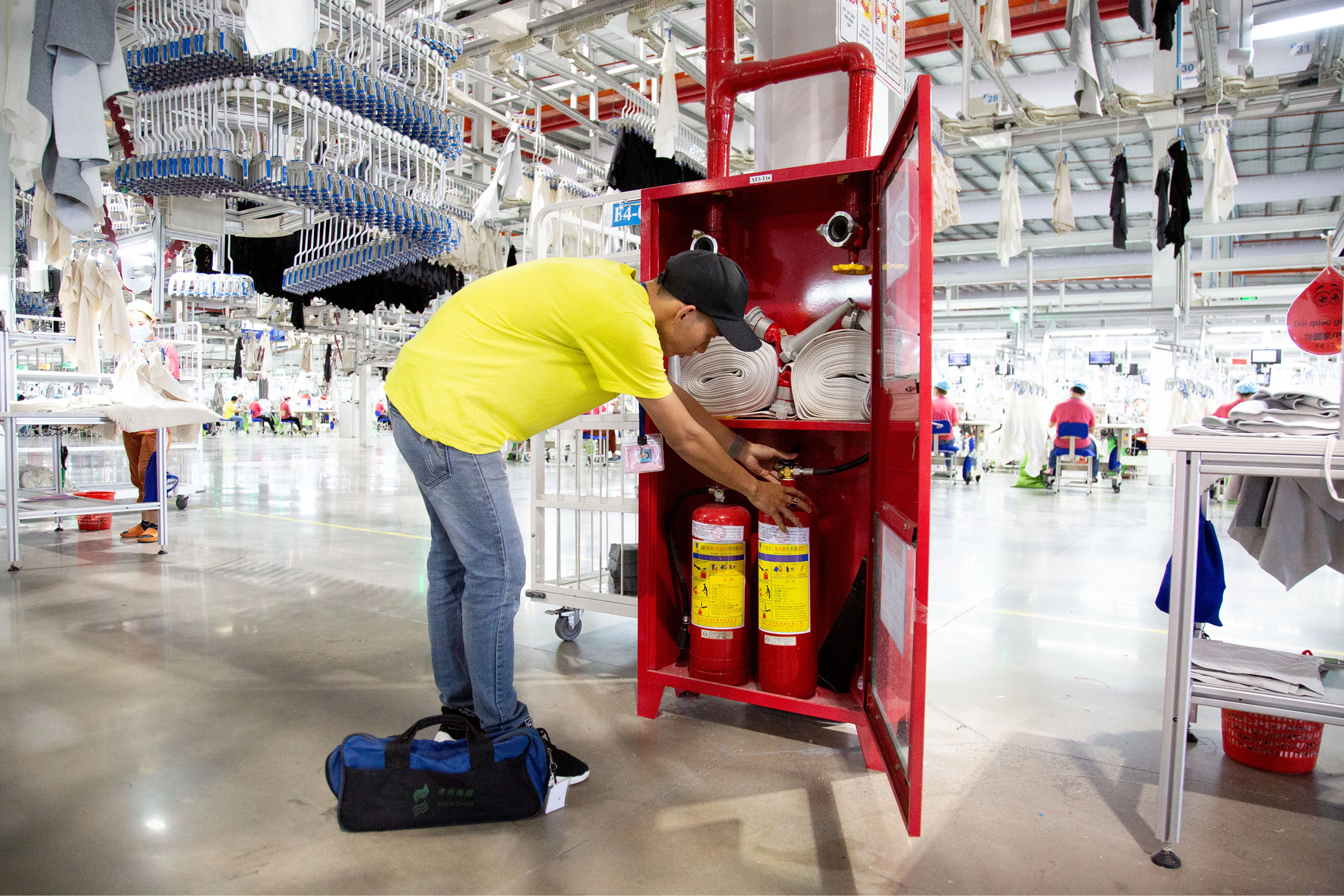
In 2018, NIKE created a culture of safety strategy and implementation program. From piloting this program, we learned that engaged and accountable leadership, coupled with a positive health and safety culture, enabled improved safety performance. Leaning on a culture of safety-focused strategy helps facility leaders communicate transformative change, empowering workers in the company to make good safety decisions. The results of the pilot can be found in a Harvard Business School case study Global Sourcing at Nike.
In FY23, we worked with the National Safety Council to analyze the societal and business impacts of our health and safety initiatives; today, we continue referencing that methodology to quantify the value we create. Part of that analysis found a 60% reduction in Lost Time Injury Rate (LTIR) from the beginning of FY20 through the end of FY24.
We are on a journey with suppliers to help develop world-class healthy and safe workplaces. To do so, we help suppliers build capabilities through our programs and then measure the maturity of their safety culture. This leads to a more resilient workforce, starting at enterprise-level before cascading to facility leadership and the individual worker. By encouraging suppliers to build a factory culture focused on safety, we can help create workplaces where everyone is accountable for driving impact.
We place a strong emphasis on leadership accountability and governance to help suppliers drive action from the top. We are investing in, and delivering, targeted systems, trainings and initiatives that guide our suppliers—and their workers—toward a stronger and more risk-resilient health and safety culture. We support suppliers in developing industry-leading health and safety management systems through three key areas: Leadership and Governance, Systems and Processes and Developing Workers.
Effective leaders set the tone. That is why we encourage leaders at the factory group level to hold themselves accountable for facility-wide safety performance and driving safe behaviors, while motivating their colleagues to do the same.
Our efforts are supported by a Transformational Leadership Program which supports suppliers in evaluating the effectiveness of their corporate safety governance structures. Administered by the Institution of Occupational Safety and Health (IOSH), the Transformation Leadership Program is delivered to enterprise-level business leaders to help them understand their health and safety obligations. During FY24, another two supplier corporate groups completed the program, bringing the current total to 14 groups representing 73 facilities.
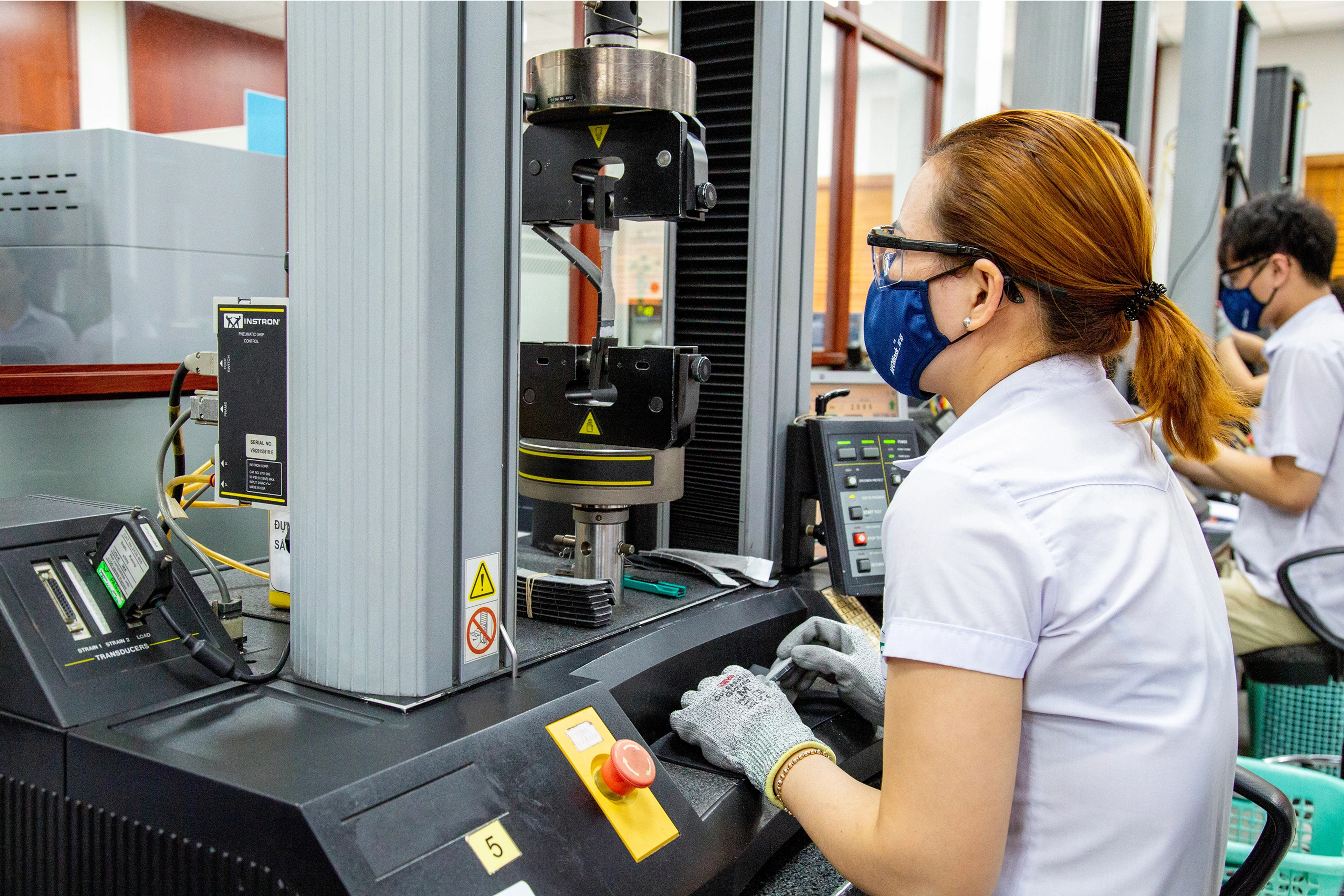
As part of a robust occupational health and safety program, we encourage suppliers to implement industry-leading systems and processes to reduce worker risk.
We are a member of the Life and Building Safety (LABS) initiative, an industry-driven program that brings together brands, retailers and public organizations to mitigate preventable fire, electrical and structural safety risks in countries that produce apparel, footwear, accessories and home textiles. Through our Workplace Safety Facilitator (WSF) program, we help workers engage with their peers to encourage collective understanding of what behaviors drives fire and building safety. As a part of this program, we trained 14,835 strategic finished good supplier personnel on the skills needed to facilitate meaningful safety conversations and coaching sessions with colleagues. By the end of FY24, these 14,835 active WSFs had trained over 650,000 of their co-workers on fire safety.
We use recognized principles of occupational hygiene—anticipate, recognize, evaluate and control—to identify, assess and mitigate chronic illnesses and disease in the workplace. We want to empower suppliers to use these four principles in the workplace, including when new materials or manufacturing processes are introduced. As of FY24, over 400 factory-based health and safety professionals have completed our Fundamentals of Industrial Hygiene training course. In FY25, we introduced more advanced industrial hygiene courses and provided additional training for high-risk suppliers. Additionally, we have developed a reference document, Nike’s Industrial Hygiene Playbook, to further guide suppliers on how to prevent chronic illnesses and disease.
Guided by the principles of the IOSH Competency Framework Program (CFP), we are focusing on helping suppliers develop key skills and behaviors within their workforce across technical, core and behavioral safety domains to drive sustainable improvements. Throughout FY24 we delivered the IOSH competency framework to 37 participants representing 17 strategic suppliers to drive greater understanding of their current technical, behavioral and core competencies in health and safety.
We measure progress and supplier safety maturity through the NIKE “Culture of Safety Maturity Assessment” (CoSMA) tool and validate it through a third-party administered Safety Perception Survey that gathers worker feedback. Recognizing that this is an ongoing endeavor, we encourage suppliers to pursue improvements through continuous self-assessment and worker validation.
The CoSMA tool allows us to measure progress as suppliers move up maturity levels, which were based off Professor Patrick Hudson’s “safety culture ladder.” This framework, which helps explore how workplaces evolve from unsafe to safe, was adapted to reflect NIKE’s specific requirements. As we work with our suppliers to continue maturing their safety culture, we’ve targeted level 3 out of 5—the point at which we see the integration of health and safety into culture, when factories have mastered the NIKE standards, are in compliance and are now implementing safety management systems.
Our capability building and cultural maturity programs, as well as the heightened level of engagement we’ve achieved through the CoSMA tool, are the culmination of years of dedicated work to drive strong supplier health and safety performance. As we continue to progress, we are also working to benchmark our work against other organizations with world-class safety programs. That is why, during FY24, we engaged the Royal Society for the Prevention of Accidents (RoSPA), a leading voice in health and safety, to assess factory performance.
As a part of the evaluation process, factories submit information on health and safety leadership, management systems, programs and impact data, which RoSPA uses to grade performance. In FY24, 64 factories submitted applications; of those, 40 achieved a gold assessment—the highest possible grade. An additional 21 factories received silver and three achieved bronze.