Foundational Expectations and Code of Conduct
We believe a world-class responsible supply chain is grounded in standards that demonstrate respect for the people who make and move our product, the principles of a healthy and safe workplace and the environment. We set clear, foundational expectations for suppliers to be in compliance across all standards of our NIKE Facility Code of Conduct (Code) and Code Leadership Standards (CLS).
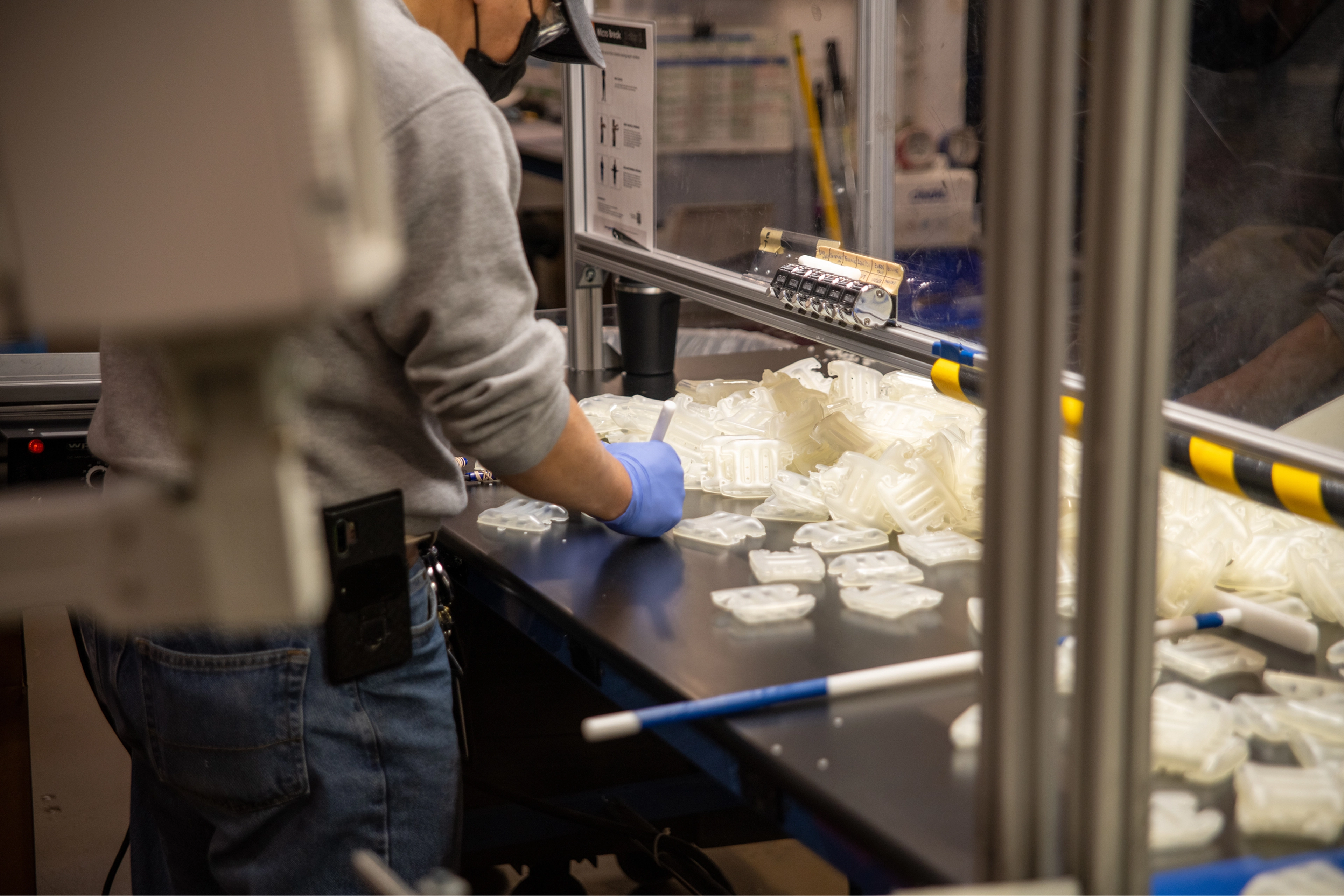
At Nike, we believe that while there is no finish line, there is a clear starting line. The Nike Code and CLS lay out the minimum standards we expect facilities to meet. These minimum standards are integral to Nike’s supplier strategies—how we evaluate baseline performance and determine the suppliers we will continue to engage with as we grow our business. We work with suppliers that share our focus on the welfare of workers, use natural resources responsibly and efficiently, manage their businesses more responsibly and sustainably and seek to move beyond minimum standards.
We expect all facilities to respect the rights of workers and advance their welfare, with particular care for people with unique vulnerabilities such as women, migrants and temporary workers. To understand and manage human rights risks and their impacts, Nike looks to the Universal Declaration of Human Rights, the International Labour Organization’s Declaration on Fundamental Principles and Rights at Work, the U.N. Guiding Principles on Business and Human Rights and the OECD Guidelines for Multinational Enterprises. We also expect suppliers to focus on areas such as emissions reduction, waste elimination and protection of natural resources. As part of Nike’s growth strategy, we seek facilities that are building agile and resilient management systems—enabling them to drive sustainable business growth, cultivate an engaged and valued workforce, foster a strong culture of safety and minimize their environmental impacts.
Nike recognizes that relationships based on clarity and mutual respect are integral to achieving our vision of a more resilient and responsible supply chain. This vision requires collaboration and joint action with facilities, other brands and all stakeholders in the shared global supply chain. We will continue to support facilities as we engage with civil society, unions, governments and other entities to affect systemic change to labor, health and safety and environmental conditions in communities where they operate.
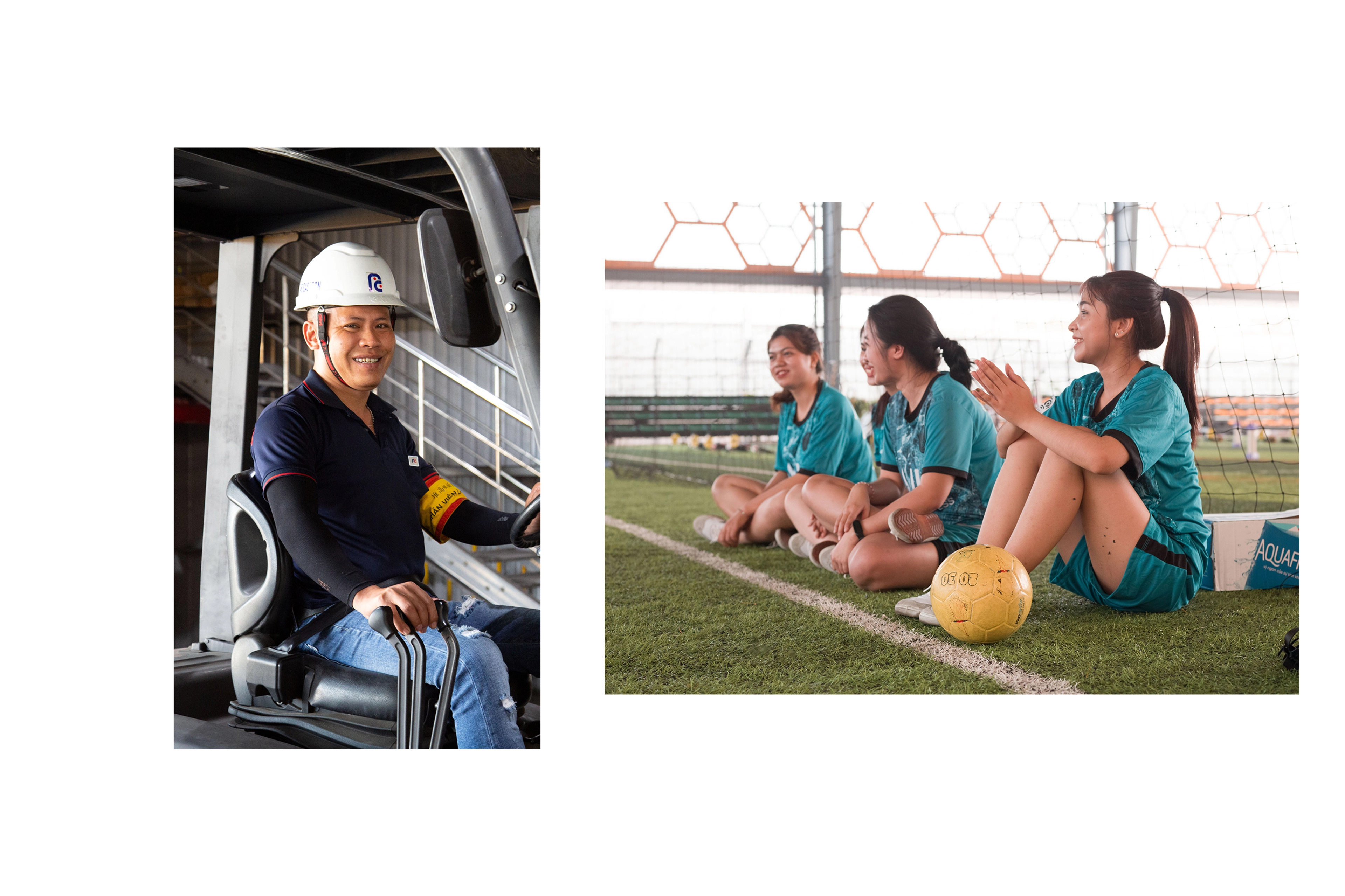
Nike co-led the development of the Zero Discharge of Hazardous Chemicals (ZDHC) Wastewater Guidelines, a collective effort of all member brands in the ZDHC Foundation to continuously work to improve wastewater discharges. Through the power of collective action, one wastewater test per the ZDHC Wastewater Guidelines is valid for all member brands of the ZDHC.
The NIKE Code sets the basis for our chemistry strategy. Based on the Code, all suppliers must properly manage chemistry and create approaches that help meeting our Restricted Substances List (RSL) and ZDHC Manufacturing Restricted Substances List (MRSL) requirements. We continue to support and drive the development of transparent guidelines, tools and training programs within our industry through work in groups such as the Apparel and Footwear International RSL Management (AFIRM) and the ZDHC Foundation. Together, these programs continue to accelerate us toward realizing the vision of zero discharge of hazardous chemicals.
All potential new Tier 1 finished goods suppliers are subject to the New Source Approval Process. Suppliers must receive an overall Bronze rating—our minimum standards—prior to beginning full production.
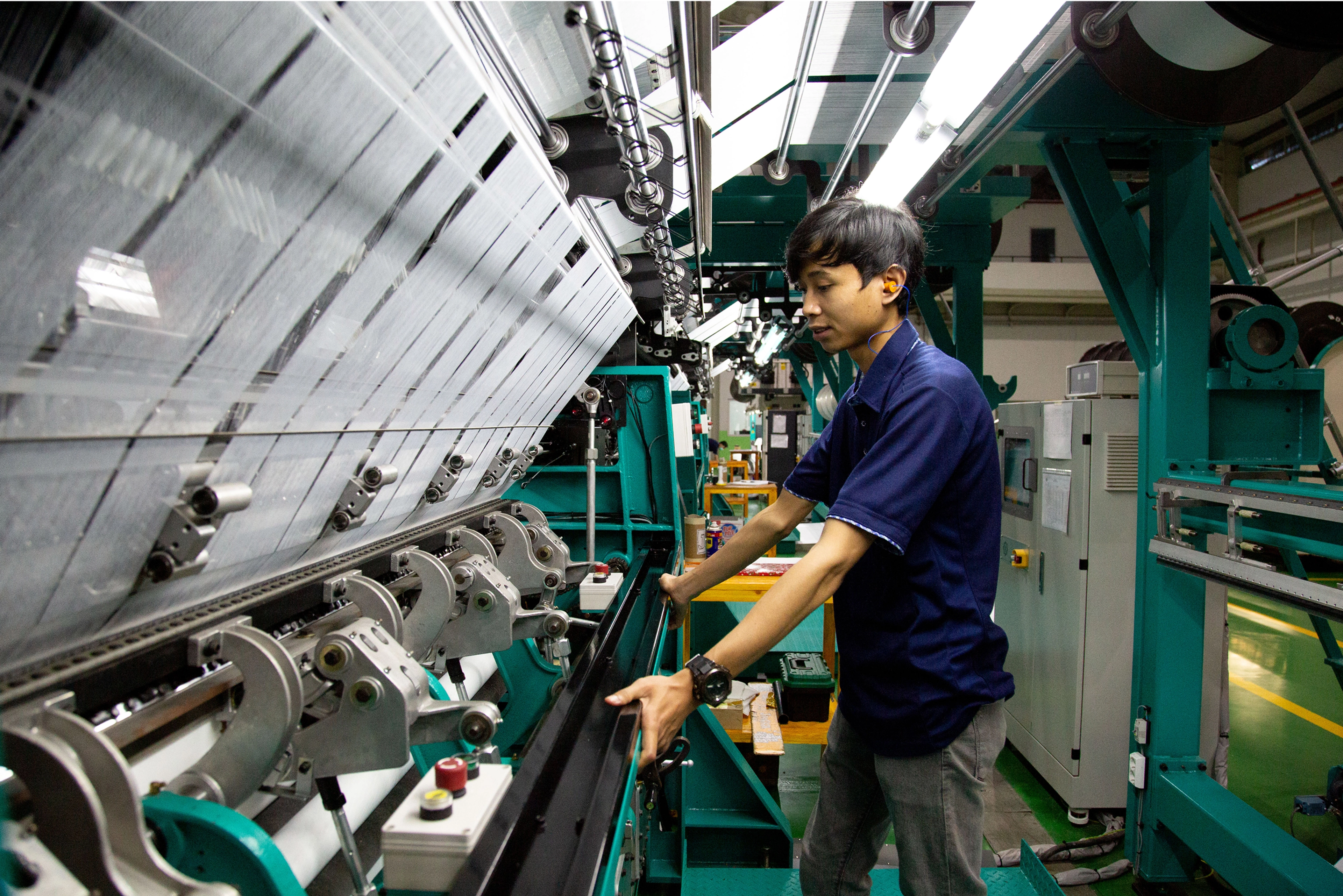
We look to recognized industry assessments to monitor facility compliance, making the shift away from proprietary assessments to minimize audit fatigue for facilities. The Social and Labor Convergence Program (SCLP) is a pioneering initiative that seeks to develop a simple, unified and effective industry-wide way to assess labor, health and safety conditions in facilities, with the goal of replacing current proprietary audit tools used by individual brands. In facilities working with multiple brands, this reduces the number of audits, increases industry efficiency, reduces audit-related costs and allows participating organizations to invest previously designated resources for compliance audits into the improvement of social and labor conditions. It is also a step in the direction of enabling a more collaborative approach to address risks and opportunities in the industry. A similar approach is taken by Cascale and the Higg Facility Environmental Module (Higg FEM) which is an industry converged tool assessing environmental performance. Nike accepts both verified SLCP assessments and verified Higg FEM assessments as well as ZDHC Wastewater tests. We are also a member of Better Work and accept Better Work audits.
We conduct internal and external third-party audits to assess compliance with Nike’s requirements and applicable laws across Tier 1 finished goods suppliers, Tier 2 materials suppliers, Air Manufacturing Innovation facilities and distribution centers. To date, we have deployed industry assessments to all applicable, in-scope facilities. We also continue our focus on targeted risk areas through unannounced facility audits.
We disclose manufacturing facilities publicly in our NIKE Manufacturing Map, an interactive map of facilities which was first published in 2005 and is updated monthly.
Nike takes issues of non-compliance seriously. If we identify an issue of non-compliance with our Code or CLS within a facility, we enroll the facility in our Targeted Remediation Program which has been successful in addressing instances of non-compliance. Should a facility fail to remediate issues identified by an assessment, audit or allegation investigation according to Nike’s requirements, it is subject to review and sanctions, including potential termination of the supplier agreement.
In the event that the relationship with an existing facility is terminated, either resulting from poor sustainability performance or other reasons, Nike begins its responsible exit process. This includes evaluation of the risks to Nike, the workers, local community and environment associated with the upcoming divestment.
This process also includes a reduction in production orders over a determined length of time to create the least amount of disruption to a business and workers as possible. In high-risk situations, multi-stakeholder working groups are assembled to develop and monitor an exit plan designed to manage the risks identified with the divestment.