
The Willy Wonka factory for innovation. The NASA of sports science. The epicentre of performance product creation. Athletes, industry leaders and visiting partners have described the Nike World Headquarters in Beaverton, Oregon, in myriad ways. Our teams like to call it their dreamland. The place where creating, designing and breaking limits to better serve athletes has no bounds. The secret rooms where the unimaginable—the future of fastest, strongest, greatest—is made real. The images below capture a behind-the-scenes look into those unknown spaces, with audio context from Nike employees who help bring the dreams to life.
The LeBron James Innovation Center is where listening to the voice of the athlete is made tangible. While athletes are observed, others are at play too: researching, testing and, yes, creating the future. The goal is to understand athletes' unique needs and opportunities, contextualise challenges and generate breakthroughs across the spectrum of play and movement in a variety of environments. Much of that action takes place in the building's top floor, the Nike Sport Research Lab (NSRL), which houses the world's largest motion-capture installation (400 cameras), a basketball court, pitch and track with 97 force plates, sweat-wicking mannequins and three environmental climate chambers that can mimic nearly any condition on Earth. Some of the innovator's prize tools: more than 80 prototyping machines that allow the Nike team to produce samples to test in under an hour.
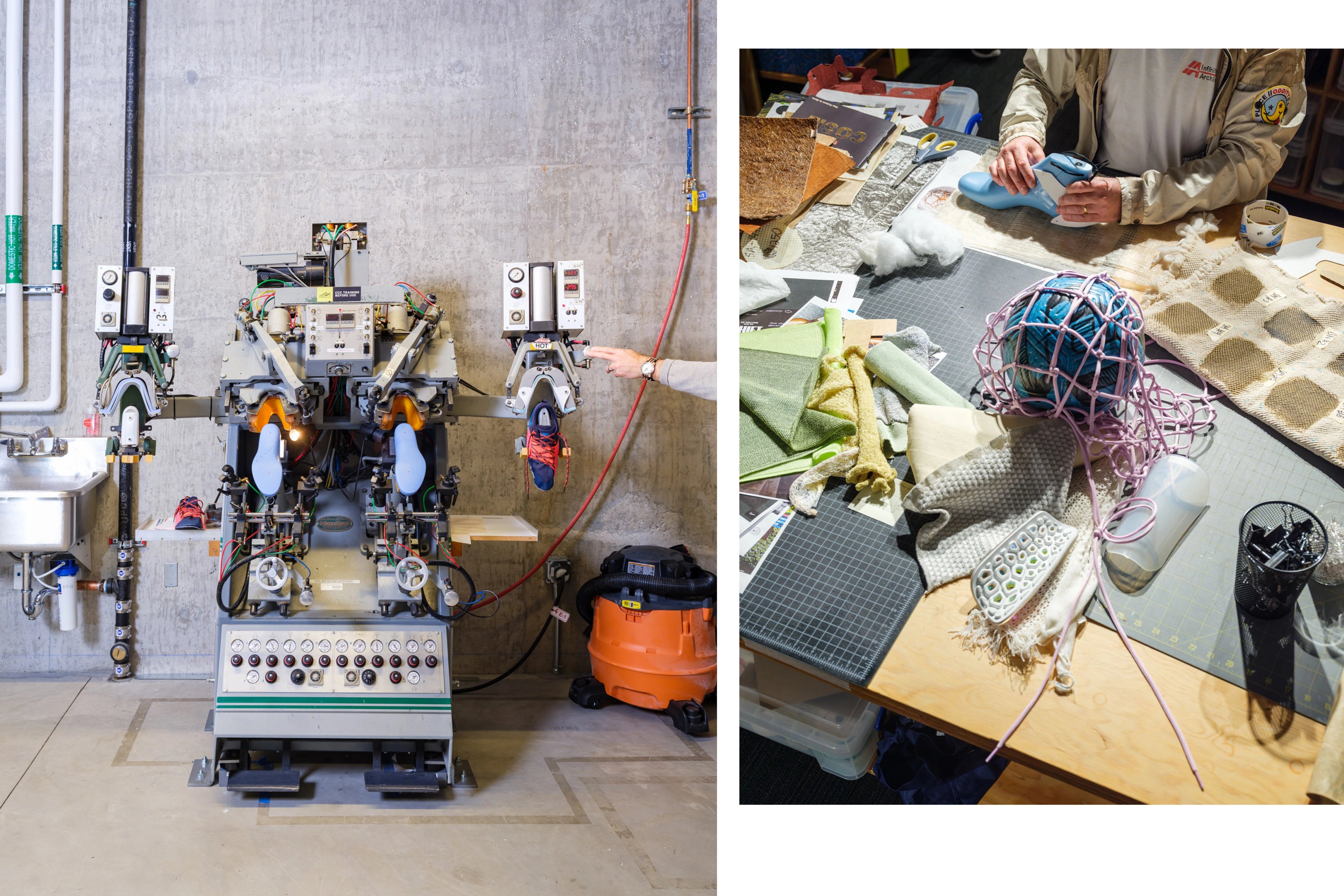
Left: The heel-shaping machine designer Noah Murphy-Reinhertz describes in the audio clip above. | Right: An unfiltered look at hands-on experimentation, as seen from Murphy-Reinhertz's desk.
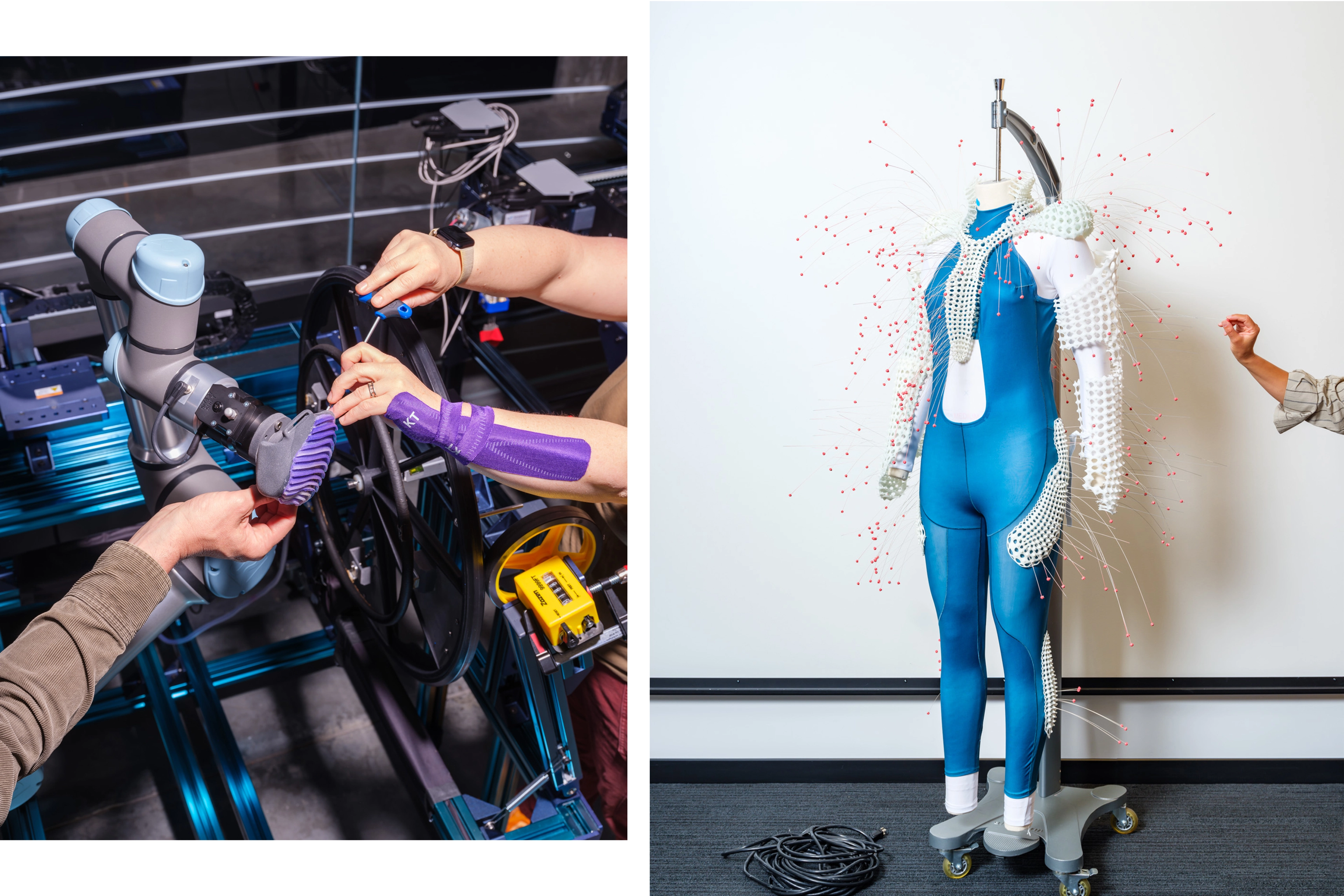
Left: Adjusting a test sample of new racing gloves for Paralympian Tatyana McFadden. | Right: A bodysuit that helps designers imagine new approaches to creating for heightened sensory perception.
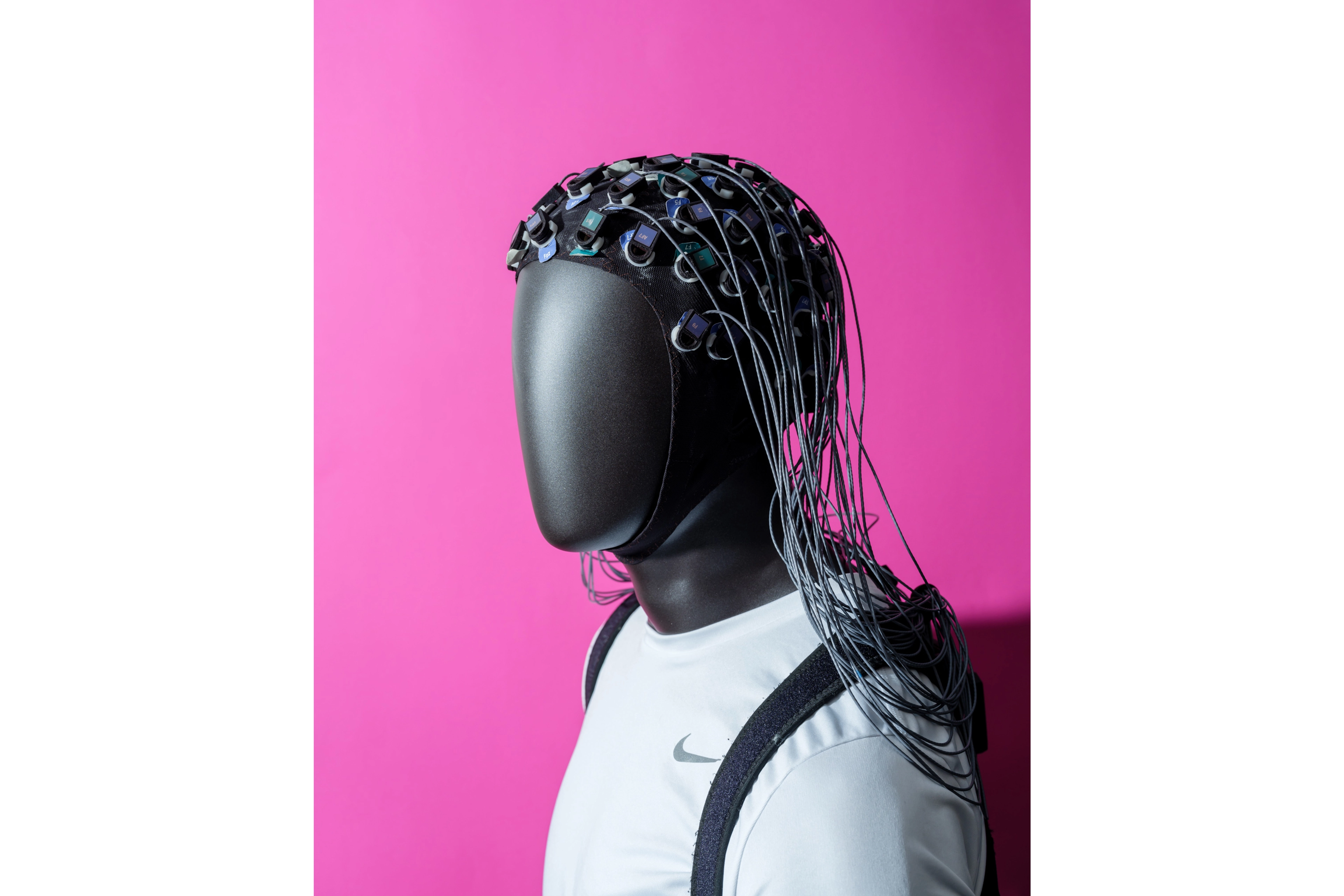
The NSRL has expanded its field of focus in recent years to include mind sciences (sensory and cognitive tasks in the brain) as a growing area of expertise.
Understanding the past can inform and inspire how we innovate for the future, and no space at Nike preserves and stokes a more thorough accounting of our heritage than the Department of Nike Archives. This 50-plus-year Nike archive is the greatest in the world. From the actual broken waffle iron Bill Bowerman made famous to the self-lacing shoes from everyone's favourite futuristic film to Serena's iconic gladiator outfit, DNA houses the tangible history—papers, posters, photographs, memorabilia and of course, shoes—that represent the culture and soul of the Swoosh.
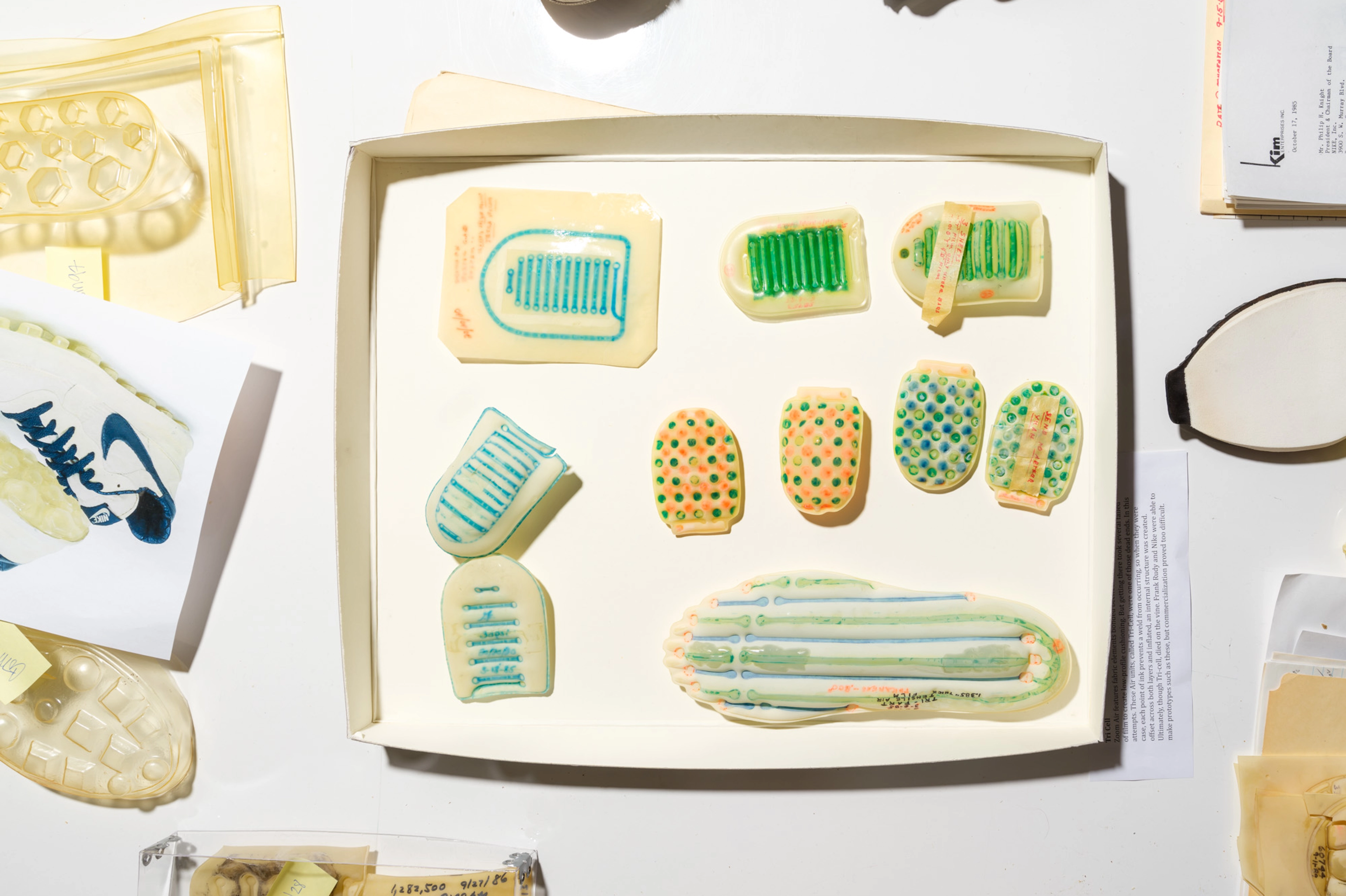
A historic example (and failure) of how to create a technology called "Tri-Cell", a predecessor to the Air Zoom unit, which used dabs of ink on polyurethane film.
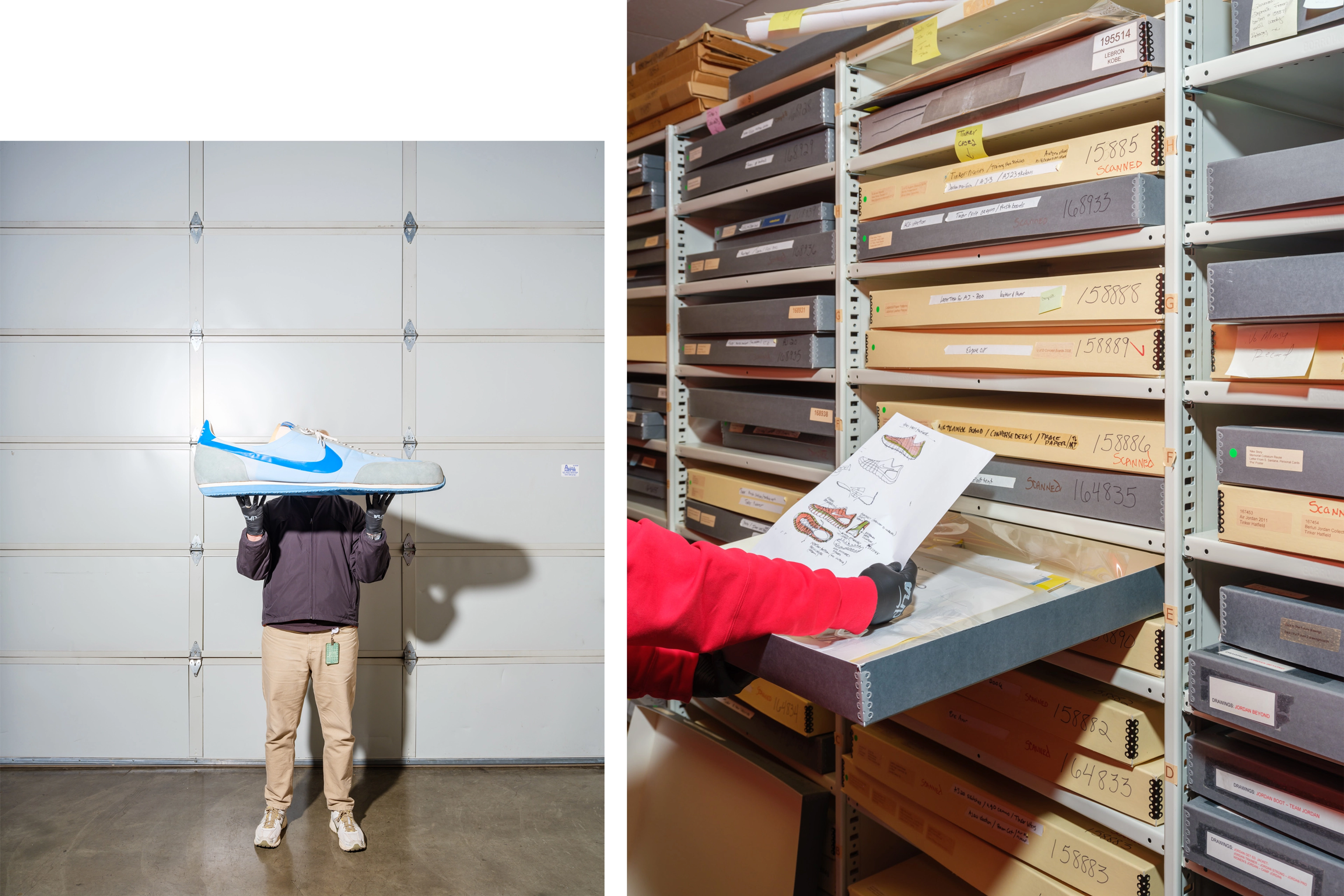
Left: A larger-than-life running shoe replica, used in a Nike retail display in the early 1980s. | Right: Sketches of the Nike Free, a seminal innovation that mimicked barefoot running.
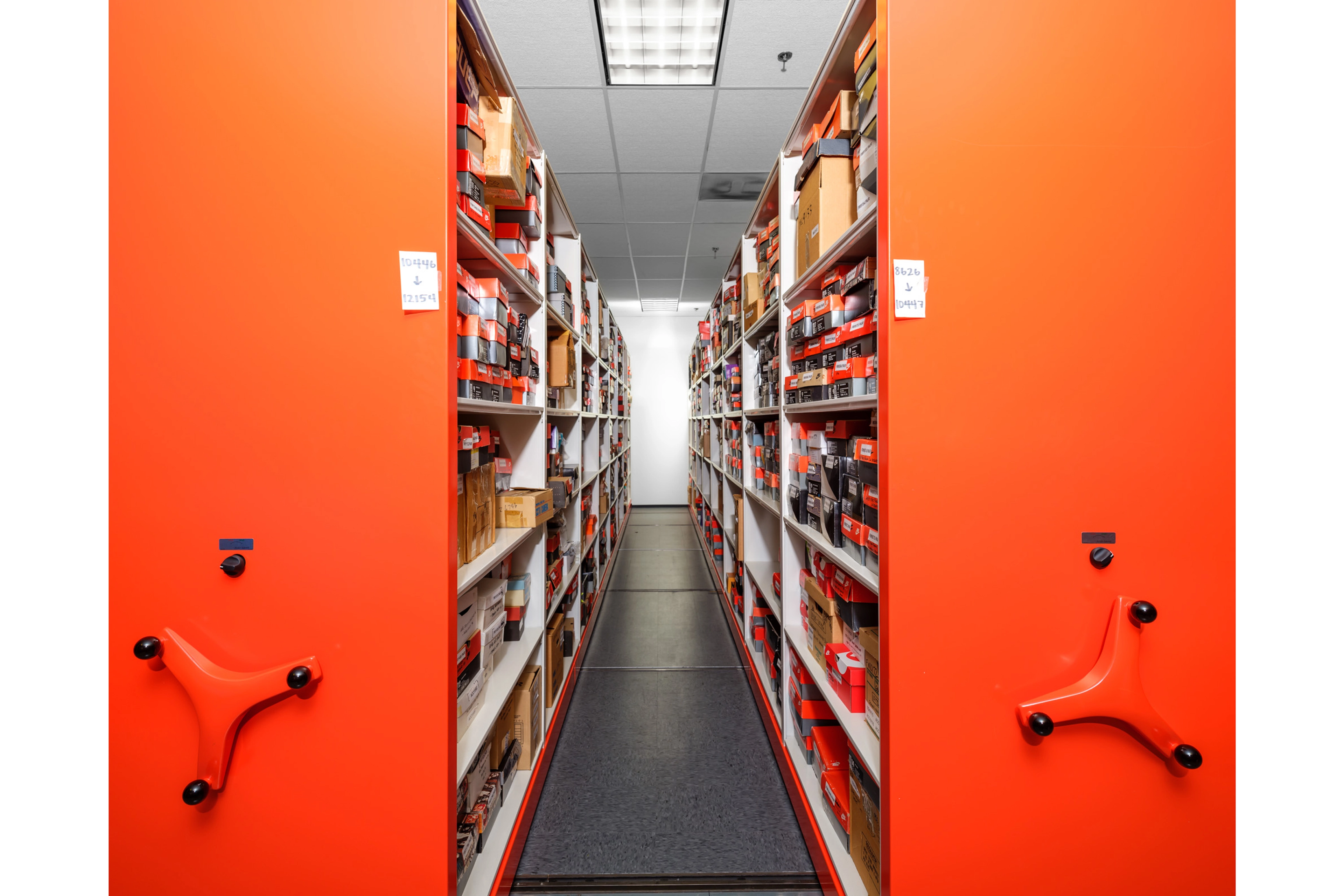
Many of the shoe boxes in DNA's rolling stacks are labelled with the names of the athletes who once wore the footwear within.
"No matter who comes in, whether it's rappers or athletes or graffiti artists ... everyone turns into a high-schooler; they're disarmed and remember that time in their lives, and they revel in the memories. People dig going down memory lane".
Matt Williams, senior manager, DNA Brand Narrative
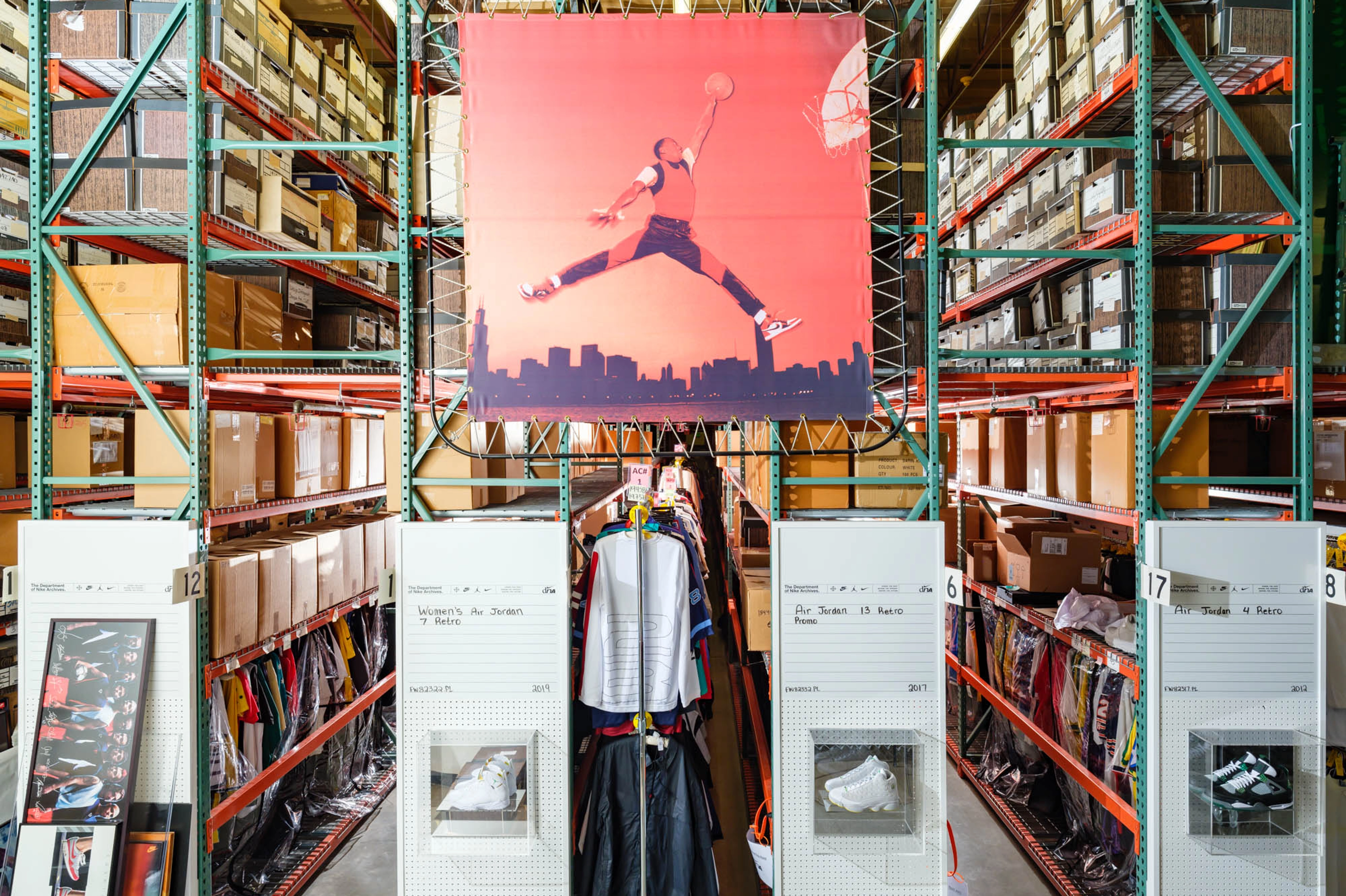
Artefacts in storage at DNA. The collection comprises over 250,000 objects and counting.
There's something magical about putting on a fresh pair of Nike Air shoes, and we think it's thanks to our unique Air technology. In just three facilities in the US—two located a mile from Nike World Headquarters—experts on our Air Manufacturing Innovation (Air MI) team make that magic happen. Air MI is where we produce the propriety TPU material that forms our Air units and where we hold 500-plus patents. It's also the place where a highly skilled team comes together to build the products that will help break sport barriers. Inside the facility are engineers with 15 specialities across them, who custom-build technology platforms and flexible, scalable production lines to deliver the exact capabilities needed to manufacture the next generation of Air. That's in partnership with skilled production teammates, trained across the line, to ensure the highest fidelity and quality of our Air units.
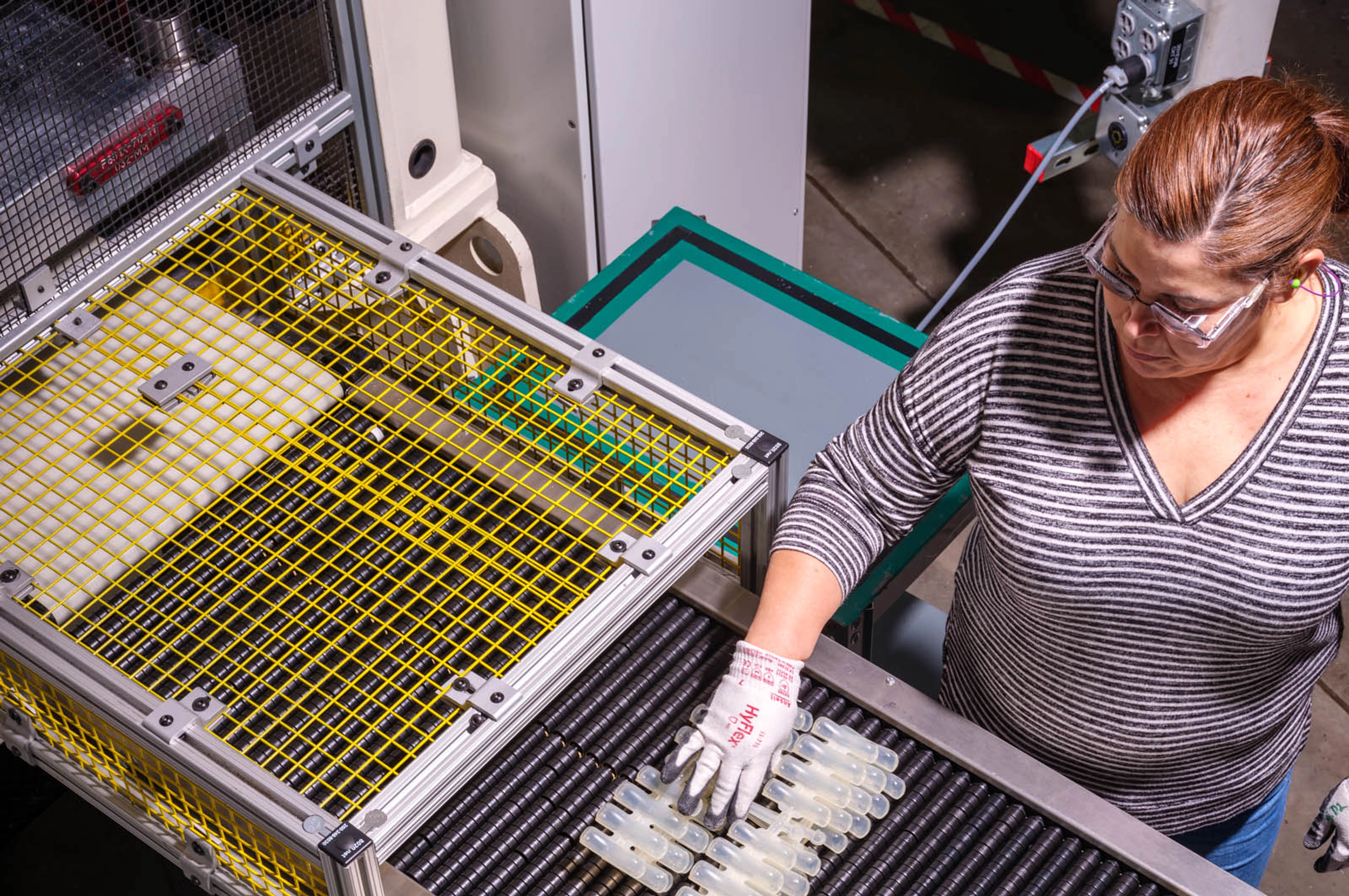
The hands-on Air-bag creation process at Air MI, explained by production manager Cassie Rigles-Kocker in the audio above.
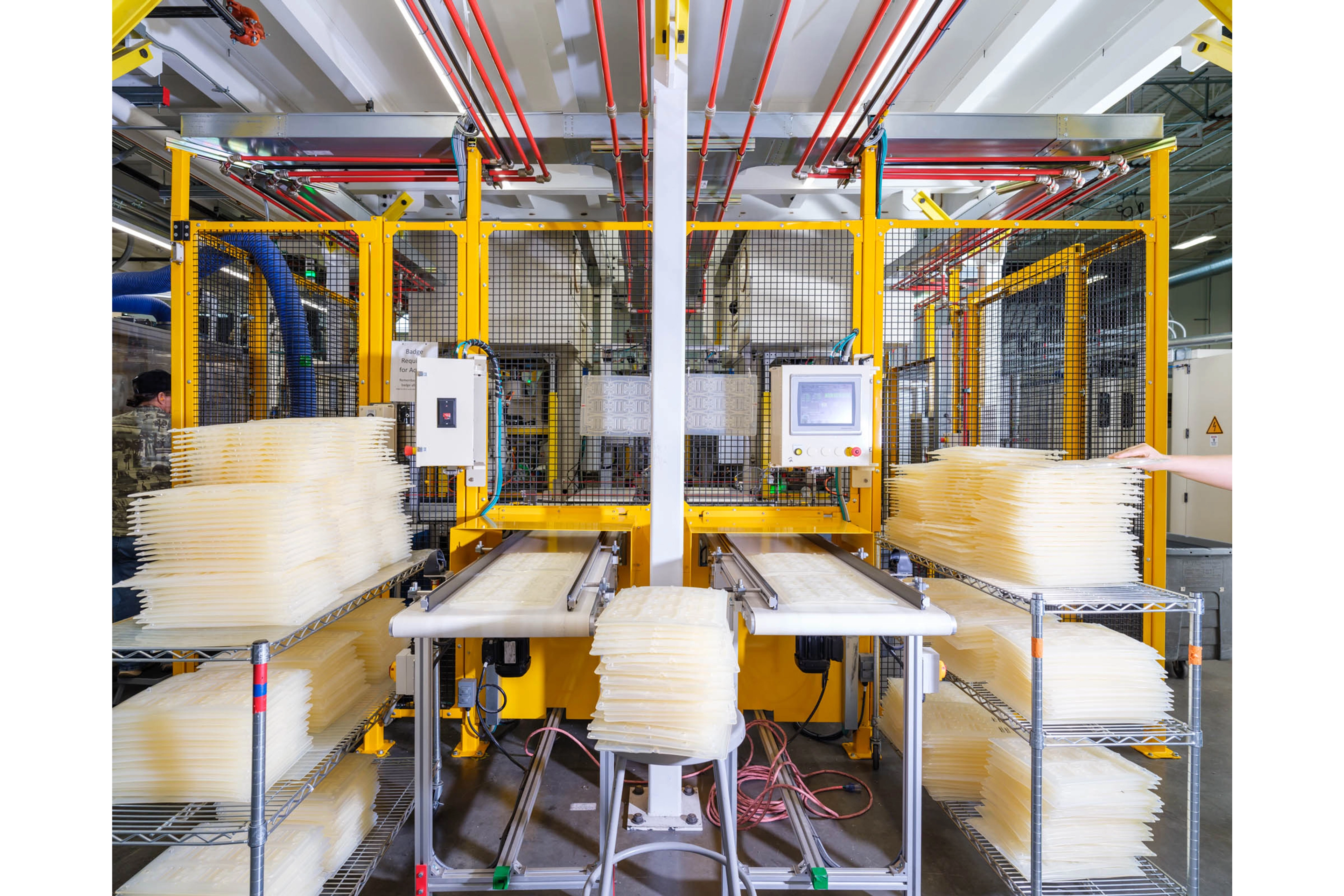
Plaques of Air unit components await inflation inside Air MI.
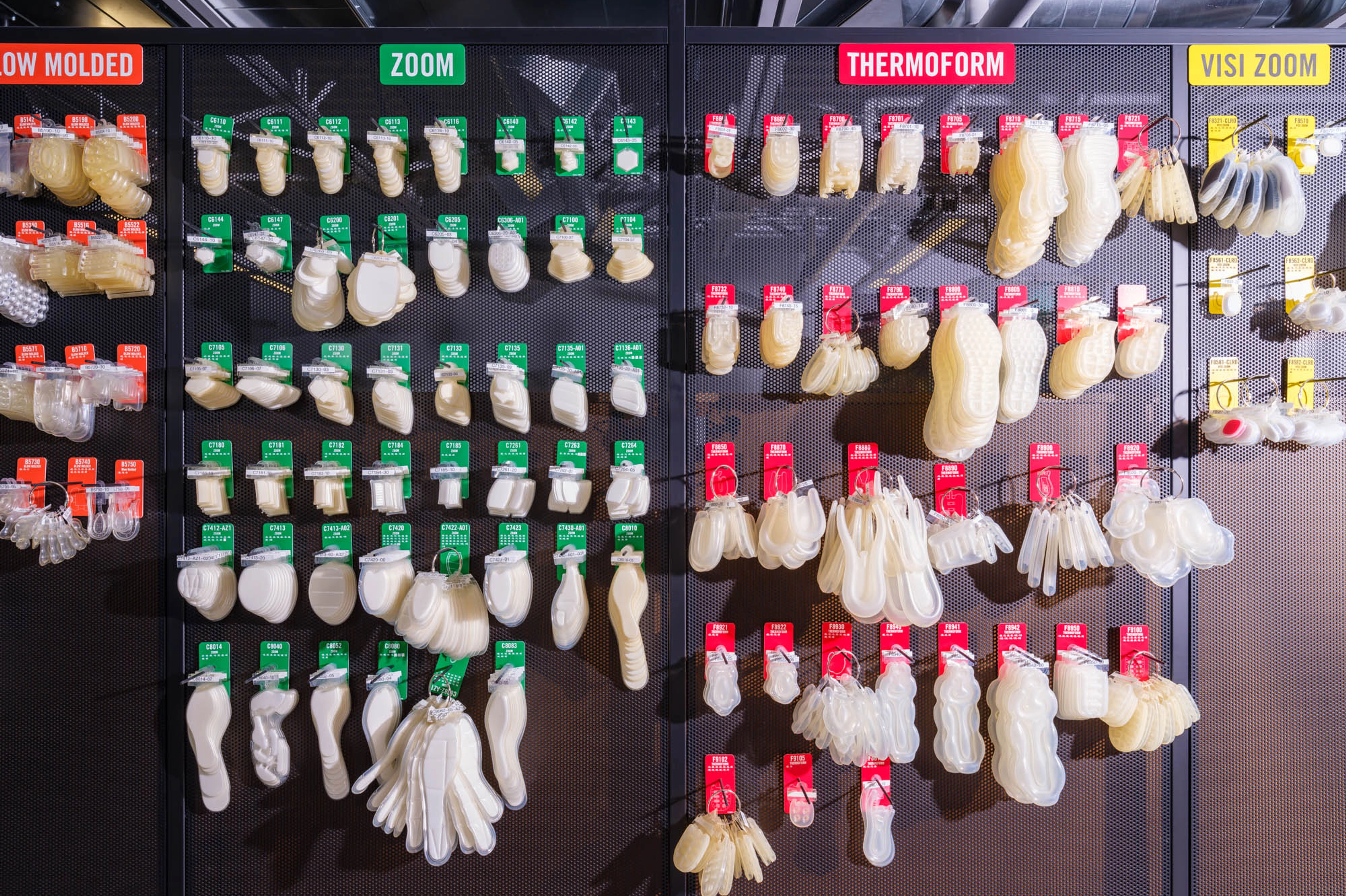
Three methods of make are used across Air MI: blow moulding, thermoforming and radio-frequency welding. Nike currently holds 500-plus patents on Air innovations.
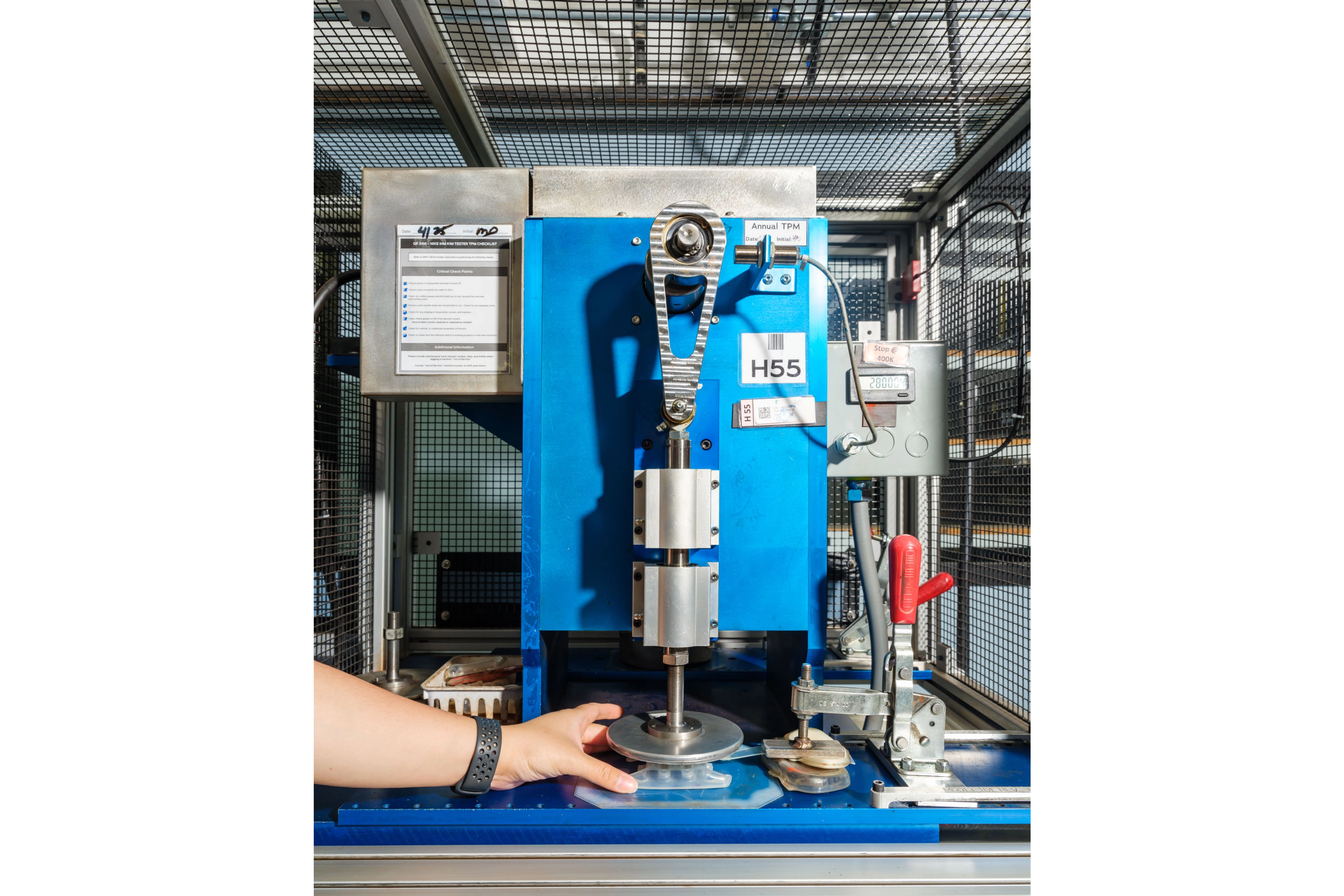
Durability testing of Air units is done on proprietary "Kim Testers", named for Frank Rudy's daughter, and explained by Air MI production manager Pat Sagebiel in the audio above.
The APCC is a top-secret, state-of-the-art facility focused on innovation in product design. Consider it the home of rapid prototyping for Nike designers, scientists and researchers who need to test, refine and create new ideas for athletes at scale. With advanced methods of make, the APCC explores more flexible and forward-looking approaches that streamline the development and manufacturing process, reducing time and effort, while pushing boundaries in sports innovation. You'll find chemical, mechatronics, process and robotics engineers, as well as machinists, all dedicated to accelerating ideas through trial and experimentation, faster and more precisely than ever before.

Left: Dusting the powder off a freshly printed prototype, as described by footwear director Holli Pheil in the audio above. | Right: A 3D printer that can produce a TPU upper from pellets.
"You can innovate and do lots of cool things, but to do it at Nike's scale is really challenging. That challenge keeps me intrigued, keeps my brain going—and having fun while we do it".
Holli Pheil, capabilities development director
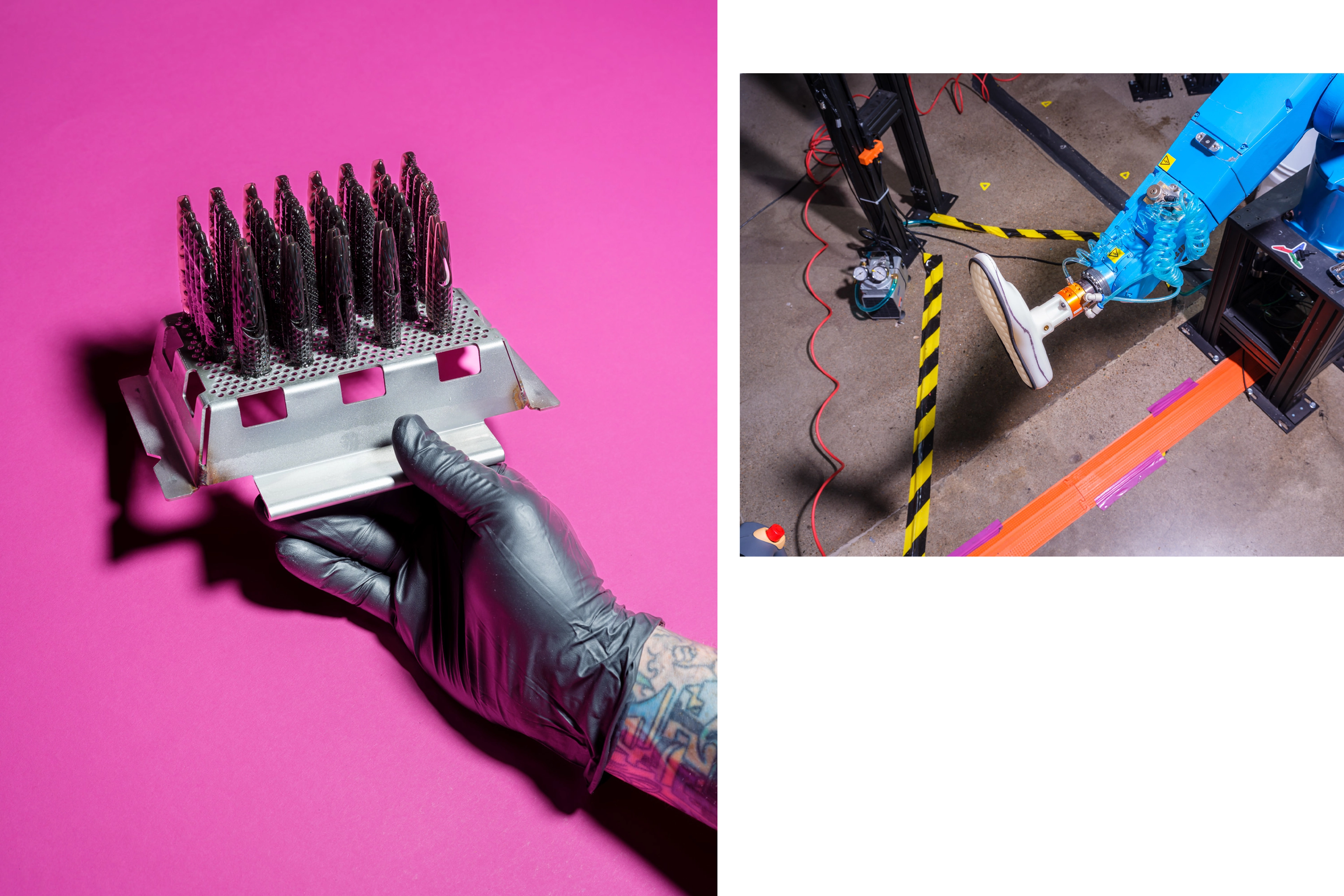
Left: The APCC 3D-printed ultra-lightweight, sport-ready nails designed for Sha'Carri Richardson. | Right: A robotic arm with a vacuum attachment to test outsoles without an upper.
Photography by Alastair Philip Wiper, shot for the "Nike: Form Follows Motion" exhibit at the Vitra Design Museum.